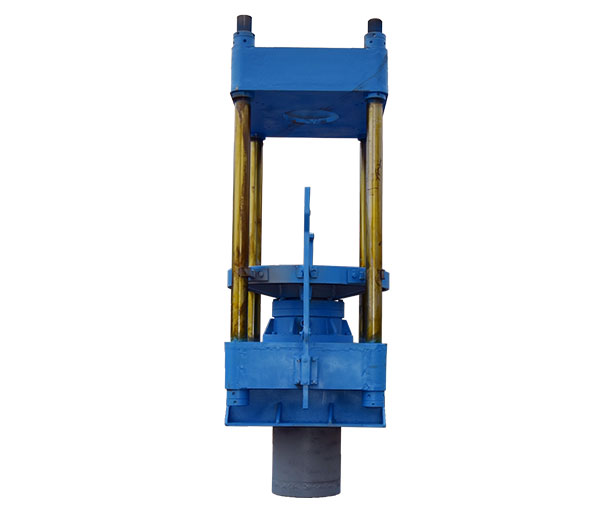
The inner tube vulcanizer is also a kind of special flat vulcanizer which adds the cushion mold and accessories. The power of the inner tube vulcanizer is oil pressure or water pressure. The cushion mold consists of the lower mold, the upper mold and the outer mold. The lower mold is fixed on the tray of the plunger, the upper mold is fixed on the upper mold beam, and the outer mold is placed on the column.
introduce
When vulcanizing, first place the circular rubber billet with square section on the lower mold, when the hydraulic cylinder pushes the lower mold of the plunger tray to rise. When the outer mold contacts with the lower mold, it will rise together. When the a rubber breaks contact with the upper mold, under the pressure of the hydraulic cylinder, the rubber breaks will be filled into the mold cavity and heated for vulcanization. After vulcanization, the plunger will borrow the self weight) to dry the mold
Press; pre heating required by rubber vulcanization process, automatic exhaust gas after feeding, pressure maintaining vulcanization, timing alarm, automatic mold opening, product molding and other functions are integrated. Generally, PLC control is adopted, with automatic and manual operation (customized according to the actual needs of users), which can record the required process flow, remote operation and system management.
The surface temperature of hot plate is uniform, temperature control, temperature controller can accurately record the temperature data, keep the pressure stable and reliable, and operate safely and conveniently. In the early stage of mass production, the commissioning time of medium and high-grade machines is short, and the equipment reliability is high. 99% of the equipment on the market is manufactured on the premise of ensuring product quality, providing production efficiency and obtaining significant economic benefits.